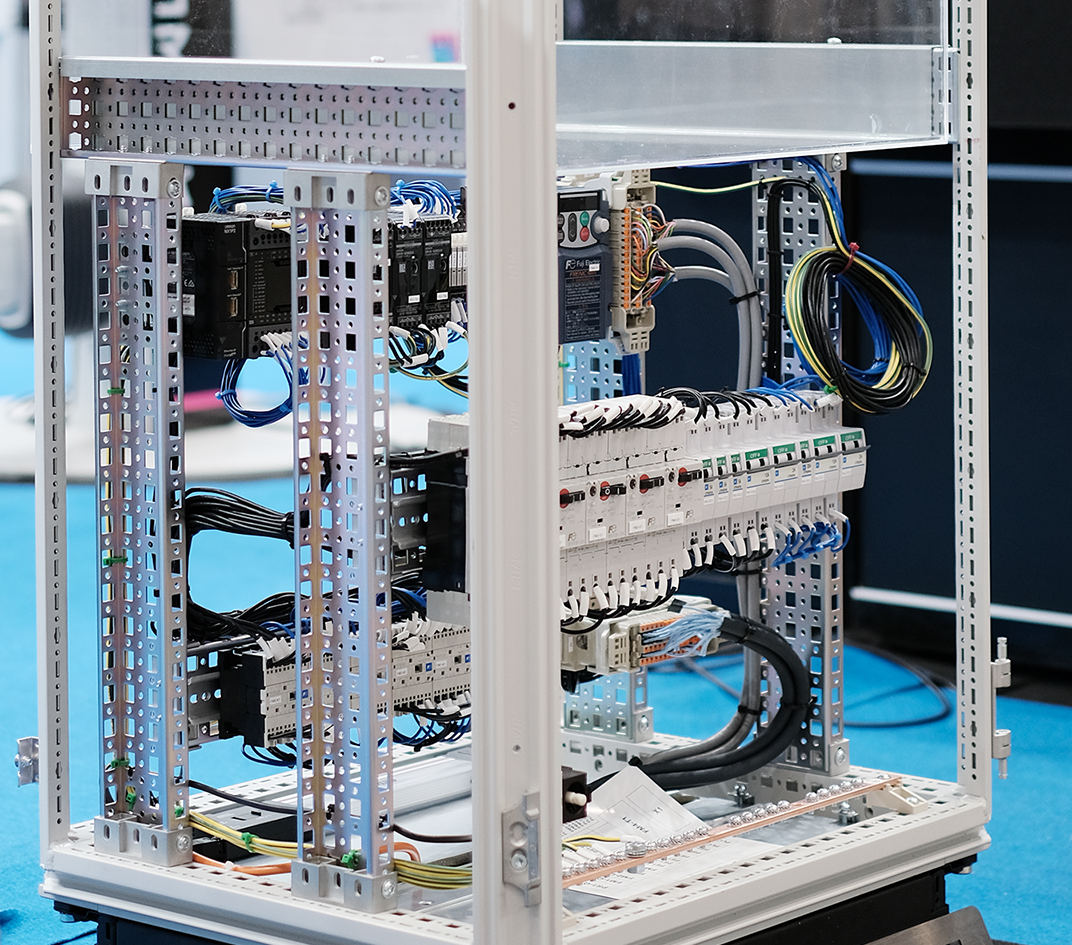
2Dから3Dへ。XYの平面世界に対し、Z軸が加わった3Dの立体世界は、より発想や行動の自由度が増し、さまざまな恩恵をもたらしています。そんな3D活用について、制御盤の世界もいよいよ3Dに突入です。
といっても3D CADや3Dデータの話ではなく、制御盤自体を3D化しようというお話。3D制御盤はこれまでとはまったく異なる構造で、制御盤の設計・製造技術のブレイクスルーになるとも期待されています。今回はそんな制御盤の最新技術である「3D制御盤」を紹介します。
3D制御盤とは?
3D制御盤とは、その名の通り制御盤の一種ですが、3D CADを使って制御盤を3次元構造で設計し、盤内機器も3次元に配置した制御盤のこと。今ある一般的な制御盤が2次元の2D構造であるのに対して3D構造を持つ制御盤として「3D制御盤」と言われます。
これまでの制御盤との違い
当たり前の話ですが、制御盤は鋼鉄または樹脂でできた頑丈な四角い箱の中に、機械に電力を供給して制御する電源や、機械の動きをコントロールする制御機器を収め、それらを電線でつないだものです。
3D制御盤もこの範疇にあり、箱の中に電源と制御機器が配置されているのは一緒。外観も従来の制御盤と変わりません。しかし内部構造はまったく異なります。
箱を開けて中身を見れば、その違いは一目瞭然。これまでの制御盤は、中板と呼ばれる平面の板の上にDINレールを取り付け、そこに電源や制御機器を組み付けて作ります。そのため機器は扉の正面にすべて配置されています。
それに対し3D制御盤は、箱の内部縦横、奥行きの3次元空間をフルに使って機器を配置して作ります。そのため箱の骨格となるフレームにDINレールがわたされ、その上に各機器が配置され、背面だけでなく、壁面や天井など内部のあらゆる面と場所に無駄なくみっちりと機器が取り付けられています。
つまりは、中板という2次元の上に機器を配置して電線でつなげ、それを箱に収めたのが従来の制御盤。箱の内部に足場を組むようにDINレールをわたして3次元に機器を配置して配線したのが3D制御盤となります。 背面から見た3D制御盤
制御盤の設計製造のブレイクスルーになる3D制御盤
3D制御盤の最大のメリットは、従来の制御盤に比べて「圧倒的に小型化できること」です。内部空間を最大限に活用できるので、自ずと小型化が可能です。その効果は、従来の2Dの制御盤とまったく同じ機器構成で制御盤を作った場合、3D制御盤はサイズを半分以下にすることができます。
長年にわたって、ユーザーや機械メーカーからは制御盤をもっと小型化してほしいという声は根強く寄せられてきましたが、すでに機器の小型化はかなりのところまで進み、レイアウト設計もやり尽くして標準化されていたため、制御盤の小型化はこれ以上難しいとされてきました。それに対し3D制御盤は、3次元で機器を配置するという常識を覆す発想により、制御盤の小型化に新たな可能性を開き、ブレイクスルーと期待されています。
3D制御盤がもたらすメリット
3D制御盤は圧倒的な小型化によって、制御盤を作る制御盤メーカー、制御盤を自社製品の機械に採用する機械メーカー、それらの機械や設備を使うユーザー企業のそれぞれに多くのメリットを生み出します。
ひとつ目が、省スペースによるTCO改善。工場や製造現場はスペースが限られていて、それをいかに効率的に使うかが生産性を高め利益を上げるポイント。そのため装置の小型化はそれだけでユーザー企業に利益をもたらします。3D制御盤で小型化することによって置き場所の自由度、選択肢は多くなり、結果として効率的な現場づくりに役立ちます。
2つ目が、小型化と高性能化の両立。機械の性能を高めようとすると制御盤に搭載する機器の種類と数が増え、それはそのまま制御盤のサイズに跳ね返っていきます。特に近年はIoTやAI活用によってこれまで制御盤には入っていなかったような産業用PCや通信機器などの新しい機器を追加するケースが増えてきています。高性能化と制御盤サイズは比例していましたが、3D制御盤にすることによってサイズはそのまま、または小さくした上に、新たな機器を追加して機能を強化することができ、生産性向上に効果的です。
3つ目がカーボンフリーへの貢献。制御盤の箱には多くの鋼材が使われ、その製造過程では多くのCO2が排出されています。制御盤のサイズが大きければ大きいほど鋼材使用量は増え、制御盤1面あたりのCO2排出量は多くなります。それに対し3D制御盤はサイズを小型化できるため鋼材使用量を減らし、CO2排出量も削減します。 3D制御盤(左)と一般的な制御盤(右)
また3D制御盤で機器を立体配置することで盤内の通気性を高め、内部の熱上昇を抑えることができます。盤用クーラーの稼働を下げることで電力消費が下がり、それはそのままCO2排出量の減少・カーボンフリーにつなげることができます。
さらに、従来の制御盤は配線を隠すためにダクトを使っていましたが、3D制御盤ではダクトも不要となります。使用部材を減らすことができ、環境にも優しい制御盤に仕上げることができます。 電線はTS 8のシステムレールに固定ですっきり
4つ目は、制御盤メーカーの高付加価値化です。いまや制御盤は、どんな制御盤であってもある程度、型が決まっていて、付加価値を付けて他者と差別化するのが難しくなっています。そのため価格が低く抑えられ、制御盤メーカーが利益を産みにくい構造になってしまっています。それに対し3D制御盤は、新しい技術で付加価値が高く、手がけられる制御盤メーカーも少なく、さらに決まった型がないので技術の差が出やすいという性格があります。3D制御盤を早くから取り組み、熟練しておくことで、制御盤メーカーは先行者メリットを享受できることになります。【3D制御盤】立体配置の盤の構造
リタールの標準キャビネットTS8とEPLANで作る3D制御盤
チャレンジングでメリットも多い3D制御盤とは言え、これまでとは異なる技術であり、いきなり設計・製造するのは難しいと思ってしまいます。しかしながら実際は、従来の2Dの制御盤設計・製造の技術があれば3D制御盤づくりはそれほどハードルは高くなく、ツールも揃っているので今すぐスタートすることが可能です。最低限必要なのは、箱にリタールの標準キャビネット「TS8」を採用し、電気設計CADはEPLANのプラットフォームを使うこと。あとはこれまでと同じように制御盤を設計製造するだけです。 TS8ー多彩な利便性
一般的なキャビネットの場合、板金加工で薄板を曲げて作られているため、中板の従来型の2D制御盤しか対応できません。それに対しリタールの「TS8」は、フレーム構造にパネルを組み込んで使う形のキャビネットで、25ピッチのレールが標準となっているため簡単にDINレールをわたすことができ、3D制御盤には最適なものとなっています。これまでに1000万台以上の出荷実績がある標準キャビネットの定番製品であり、サイズも種類も数多く揃っています。リタールWEBサイトやEPLANのライブラリのなかから要望に合ったものを簡単に選んで図面に落とし込むことができます。
また、3D制御盤のレイアウト設計は、電気設計CADのEPLANが対応しています。電気回路図(2D)から3Dレイアウトへ容易に、EPLANプラットフォーム上でシームレスな部品配置の図面データを作成できます。これまで通りの中板に配置する2D制御盤のレイアウトでも3D制御盤レイアウトでも同じ回路図を使うことができます。筐体が変わっても3D上で部品を再配置し、ドラッグ&ドロップしなおすだけで簡単に変更でき、部品の干渉チェックや最適な配線ルートの計算もできます。
これまでに作った図面も3D制御盤に対応できるので、イチから3D制御盤用の設計に試行錯誤することなく、これまでの回路図資産を活かしながら、小型化や3D制御盤づくりを始められます。
リタールとEPLANでは、3D制御盤の設計・製造にチャレンジしたい制御盤メーカー、もっと小型化した制御盤を使いたい、3D制御盤という新しい技術で付加価値を高めたいという機械メーカーやユーザーに対し、3D制御盤の設計・製造のサポートを行っています。この機会に、ぜひ3D制御盤にチャレンジしてみませんか?
3D制御盤まとめ
海外はもともと工場の敷地が広いため、小型化や省スペース化に対する関心や要求はそれほど高くありません。しかし日本の製造業のお客様は、工場内のスペースを無駄なく使って生産性を高めたいという声が昔から強くあります。そういった中で制御盤関連メーカーとしてお客様のニーズにお応えできるのが「3D制御盤」です。
フレーム筐体のリタールのTS8の特色を生かし、標準アクセサリーを駆使すると機器の3D配置(XYZ)が簡単にできて、フレームに渡した梁(レール)に電線を束ねてダクトレスにすることも可能です。このようにキャビネットにTS8を使用することで、日本独自の制御盤製造文化「図面引いて製作板金」の作業自体が一切なくなります。また、TCO改善は万国共通の課題であり、将来的に3D制御盤が海外でも広まって標準化していく可能性は十分にあります。3D制御盤の先駆者になることで、国内はもちろん海外へもビジネスチャンスは広がっていきます。
3D制御盤を360度方向から見てみよう!
YouTube RittalJapanチャンネル【3D制御盤】立体配置の盤の構造
3D制御盤の資料ダウンロードはこちら