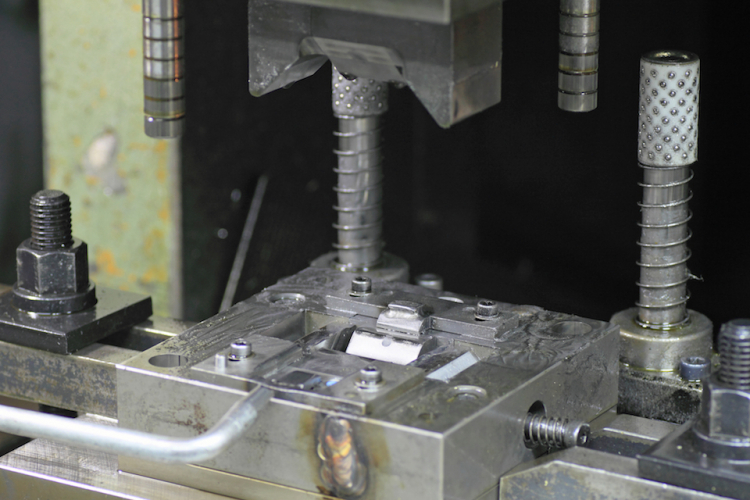
制御盤に必要となる、制御機器を収納する箱状の容器である筐体(キャビネット/ボックス/エンクロージャー)。このうち、金属製の筐体はどのような工程を経てつくられているのでしょうか。金属製筐体の製作工程とその注意点、筐体板金業界が抱える問題に触れてみます。
箱状の板金である制御盤用筐体の製造工程
制御盤の組み立てでは、筐体に取り付けていくところから始まります。では、機器を取り付けるための筐体はどのようにしてつくられているのでしょう。金属製筐体の製造工程の一例を紹介します。
- 設計
制御盤の製作仕様書をもとに、筐体の立案設計を行います。外形図・筐体工作図・内部詳細図・配線接続図・ケーブル経路図などをおこします。 - 切断
設計図をもとに、筐体を展開した状態の形状を切り出します。パンチプレス機により薄鋼板(うすこうはん)からせん断加工します。
曲げ
せん断によって型抜きされた鋼板に、プレス機またはベンダー機を用いて曲げ加工を施します。この工程により材料は箱状の形になります。 - 溶接
曲げ加工された部材を箱形状に固定するため、あらかじめ設計された固定箇所を溶接により接着します。スポット溶接と呼ばれる方法が広く使われています。 - 穴加工
ケーブルを通すためのブッシュやスイッチ・計器類を埋め込むための穴を開けます。またネジ固定のためのネジ山加工、バリ取り・研磨などの仕上げ工程もあります。 - 洗浄
溶接時の焦げや穴加工時の切削油、またバリや金属粉などを洗浄して落とします。 - 表面処理
塗装やメッキなどの表面処理を行います。 - 組み立て
最後に扉や取り付け板、フレームなどを組み立てて完成です。
箱状の板金である制御盤用筐体を設計する際の注意ポイント
このように多くの工程を経て製造される筐体ですが、実際に制御盤として製作されるのはここから先が本番です。このとき、筐体がしっかり設計されていなければ、その後の制御盤製作工程を止めてしまうことにもなりかねません。
筐体の設計時には、特に次のような点に注意しましょう。
-
寸法(公差・精度)
切断・曲げの加工時、プレス加工の特性から寸法が変化してしまうことがあります。現在ではかなりの高精度で加工することが可能ですが、ある程度の公差(許容される誤差の範囲)を設定しておきましょう。 - 逃がし
穴の変形や材料の割れといった板金上の代表的なトラブルがあります。設計時に逃がしを設けておくことで、これらのトラブルを防ぐことができます。 - 使用環境
筐体の設計にあたっては使用環境の念入りな調査が必要であり、環境に応じて構造を変えなければなりません。屋内・屋外どちらで使用するのか、また屋外であれば屋根はあるのか、直射日光は当たるのか、潮風の影響はあるのかといった事項について調査が必要です。調査の結果により防塵(ぼうじん)・防水の必要性と性能を考え、材質や表面処理方法、穴部分へのシーリングの必要性などを考慮しなければなりません。 - フレーム構造
制御盤の大きさと重量によって、フレーム構造とするか、フレームなしで鋼板だけの箱状とするかを判断する必要があります。大きく重い制御盤をフレームなしでつくった場合、吊り下げの際にアイボルト取り付け穴から鋼板が裂けたり、天井が変形したりといった危険があります。フレーム構造にするとコスト・重量ともに増加しますが、このような危険を回避可能です。ある程度の大きさになる制御盤は、フレーム構造で設計することも考慮しておきましょう。
箱状の板金を加工する際の注意ポイント
板金加工時には、それぞれの工程に発生しやすい問題があります。代表的なトラブルとその対策は次のとおりです。
抜きの注意点
パンチプレス機による抜き(せん断加工)を行う場合、板厚方法に力が発生するため材料の肉逃げ(変形)が起こる場合があります。精度を要する穴は後工程で加工したり、穴同士を板厚の2倍以上離したりといった工夫が必要です。
また、抜きによって発生した縦バリが次工程でつぶれ、横バリとなった場合に穴寸法が変わってしまうこともあります。この場合、金型側にバリをつぶさないための逃がしを設けることで解決できます。
抜き加工で避けて通れないのが、材料のそりです。そりの大きさを決定する応力は、パンチとダイ(パンチの受け側)のクリアランス、金型構造によって異なりますが、そりを小さくする方法はあります。ストリッパの押さえ力を強くする、パンチの刃先を研磨し切れ味を向上させるなどの方法がそりの減少に効果的とされています。
曲げの注意点
曲げ加工の際も、板厚により圧縮と引張の応力が発生し、板端や曲げ部分に近い穴への材料逃げ、側面方向への膨らみなど、さまざまな変形が起こる可能性があります。
曲げ部分に近い穴に材料逃げが予想される場合、曲げ線上に逃がし穴をあらかじめ開けておくことで穴の変形を防ぐことができます。
また、曲げ線と曲げ線が接する角部分、曲げ線と外形線が一致するT字型の部分などは、曲げ位置と板厚の関係から材料の割れが発生しやすくなります。この場合も、曲げ線の交差部分や曲げ線の両端に切り欠き状の逃がしを設けることで、対処することができます。
溶接の注意点
溶接にもさまざまなトラブルが発生する可能性があります。代表的なスポット溶接の不具合には、打点欠損・はがれ・割れ・打点位置ずれ・圧痕(あっこん)異常などの発生があります。また溶接全般にある不具合として、溶融面積不足・溶け込み不足・バリ・散り・ブローホール・ピットなども同様に起こる可能性があります。
これらを防止するためには、スポット溶接の4大条件といわれる次の要素を適切に設定して作業する必要があります。
- 溶接電流
電流が少ないと溶着力が弱く材料同士が離れてしまいます。電流量を増やすとナゲット(溶接部)面積が増加し溶着も強くなりますが、スパッタ(溶融金属の微小粒子)の飛散が増加します。 - 電極加圧力
大きなナゲットをつくるためには加圧力も大きくする必要があります。しかし加圧力により材料の接触抵抗が変化するため、電流と通電時間が一定のときに加圧力を大きくすると、溶着強度は下がります。 - 通電時間
通電時間が長ければ材料の溶着力は大きくなりますが、熱影響による材料のヤケや変形の可能性も高くなります。また電極チップの消耗も早まるほか、機器の損傷へとつながるおそれもあります。材料の板厚や熱伝導率によって判断する必要があります。 - 電極チップの先端形状
電極チップは材料を加圧しながら溶接電流をチップが接する面積に集中させる役割を持ちます。チップの先端径が大きすぎると電流密度が低下するため溶着力が小さくなります。しかしチップの先端径が小さいと溶着力は増しますが、溶接面積不足となる可能性があります。チップの形状は鋼板の材質や溶接角度、冷却効率などを考慮して選定する必要があります。
制御盤用筐体の板金業界が抱える問題
このように高い技術と精度が求められる筐体の板金加工ですが、業界が抱える問題も表面化しつつあります。
箱状の板金である制御盤用筐体の需要が変化していく時代へ
制御盤の筐体について、製作工程の流れ、設計時と板金加工時の注意点について紹介しました。
制御盤の筐体は、設計から板金、塗装まで多くの手間がかかっています。後継者不足・納期の問題といった時代背景を受け、標準品・既成品の筐体需要が高まっていくと予想されます。
リタールでは、様々な国際規格に準拠した制御盤筐体をご用意しています。自社で制御盤を開発する際には、リタール製の制御盤筐体を活用することで、より合理的な製作が可能です。コストカットや短納期に対応した標準筐体を数多く取り揃えておりますので、検討の際にはぜひリタールにお問い合わせください。
<盤の設計製造効率化を実現するバリューチェーン>
リタールの技術ライブラリ
「規格に適合したスイッチギア及びコントロールギアの製作IEC 61439適用」
本冊子は、新規格IEC 61439 準拠に必要な様々な対策を講じる上でのお手伝いをするために作成しました。リタール製規格適合システム製品の利用に関するご相談から貴社機器の要求設計や日常検査のご提案まで、幅広くご利用ください。
※新規格IEC 61439における変更点の他、「設計検証報告書」の作成方法などについて、85ページにわたって解説しています。
参考: